Laminated Kuusamo Log Houses walls showcase what Pölkky can do.
One of biggest strengths of Kuusamo Log Houses is the durable and strong northern timber they use as their construction material. Pölkky Oy, the maker of the high-quality laminated logs, is the largest private wood processor in Northern Finland, but how does wood get from the forest to building material used by Kuusamo Log Houses?
– It takes a tree about six to seven weeks to go from felling to becoming wall material for a Kuusamo Log House, says Pölkky Oy Development Manager Arto Airisniemi.
Airisniemi knows what he is talking about, as he has been employed by Pölkky since 1987. Starting as a temporary summer worker driving a loader, he has since worked as a local sales representative, shift supervisor, processing supervisor, and production manager.
Pölkky Oy has centralised their saw operations in at two Kuusamo facilities and at their Taivalkoski and Kajaani facilities. Their timber sourcing area is Northern Savo and Northern Finland north of Oulu. The company is committed to working for the environment, and their sourcing has received an environmental certificate.
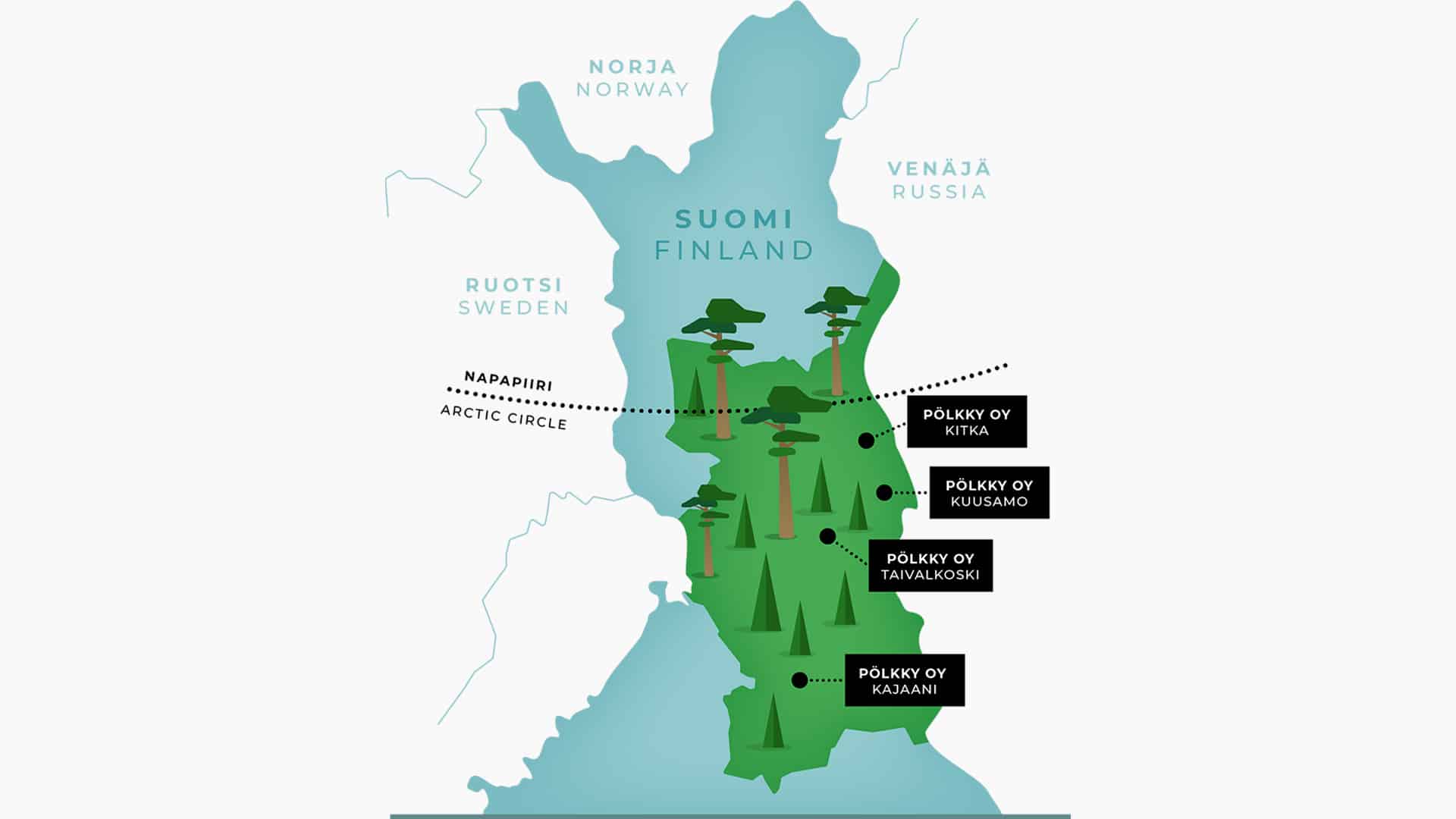
Why should you choose a log home? Read more in our blog.
STARTING WITH SORTING
Each tree is unique, so the valuable material needs to be sorted carefully along the process.
– The logs used to make laminated logs are sorted by size in the forest first, and then by their branches, length, and crown diameter into various quality grades at the sawmill, Airisniemi says.
– Branch size plays an important role, because it affects the strength of the timber. Size matters when it comes to for example construction grade timber, because the classification standards are tight, Airisniemi explains.
To put it roughly, grade AB logs are used for carpentry products, patio products, and interior decoration products for construction. Grade C logs with more branches are used for instance as massive logs where branch size is less important.
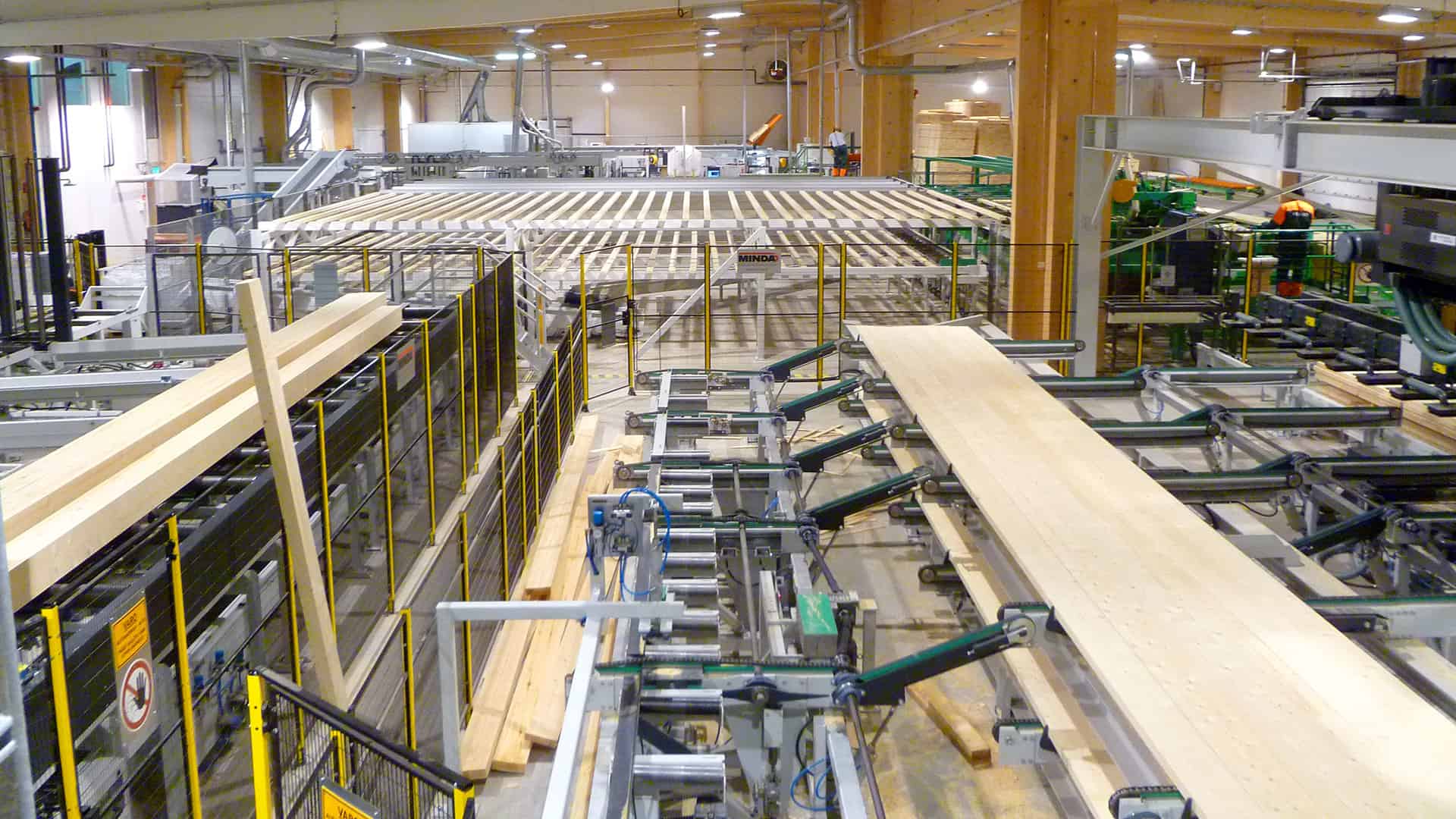
– Construction standards determine the required strength classes, because walls, frames, and roofs all have their own strength requirements. We use strength sorting machines at all of our facilities to sort the timber according to given standards. Machine operators possess visual strength grade sorting rights, so they can supervise and check the sorting done by the machines.
FROM DRYERS TO MACHINE SORTING
After sorting, the logs in the desired quality grade are sawed down to their specified width, and the resulting batten packages are taken into a dryer. The planks in the tall batten packages are dried to a moisture level specified by their final use purpose.
– The drying time depends not only on the strength and drying location of the wood, but also on the wanted moisture level. Average drying times vary from 120 to 200 hours.
After drying, the timber is allowed to sit for one to three days, after which it is ready for sorting.

– We speak of surface layers, core wood, and inner layers in connection with machine-based sorting. There are also pieces that cannot be used for gluing for whatever reason, and these are separated for other uses, Airisniemi explains.
GLUING MAKES A LAMINATED LOG
After all the precise work stages, it is finally time for gluing. First, the planks are glued into 12-metre bars using finger joints. At the same time, it is ensured that only good quality material free of fractures and bothersome branches is selected for gluing. This is followed by the actual gluing, where the finger-jointed extensions are glued into laminated logs. Kuusamo Log Houses use differently sized logs in their production, but it usually takes five or six planks to make one laminated log.
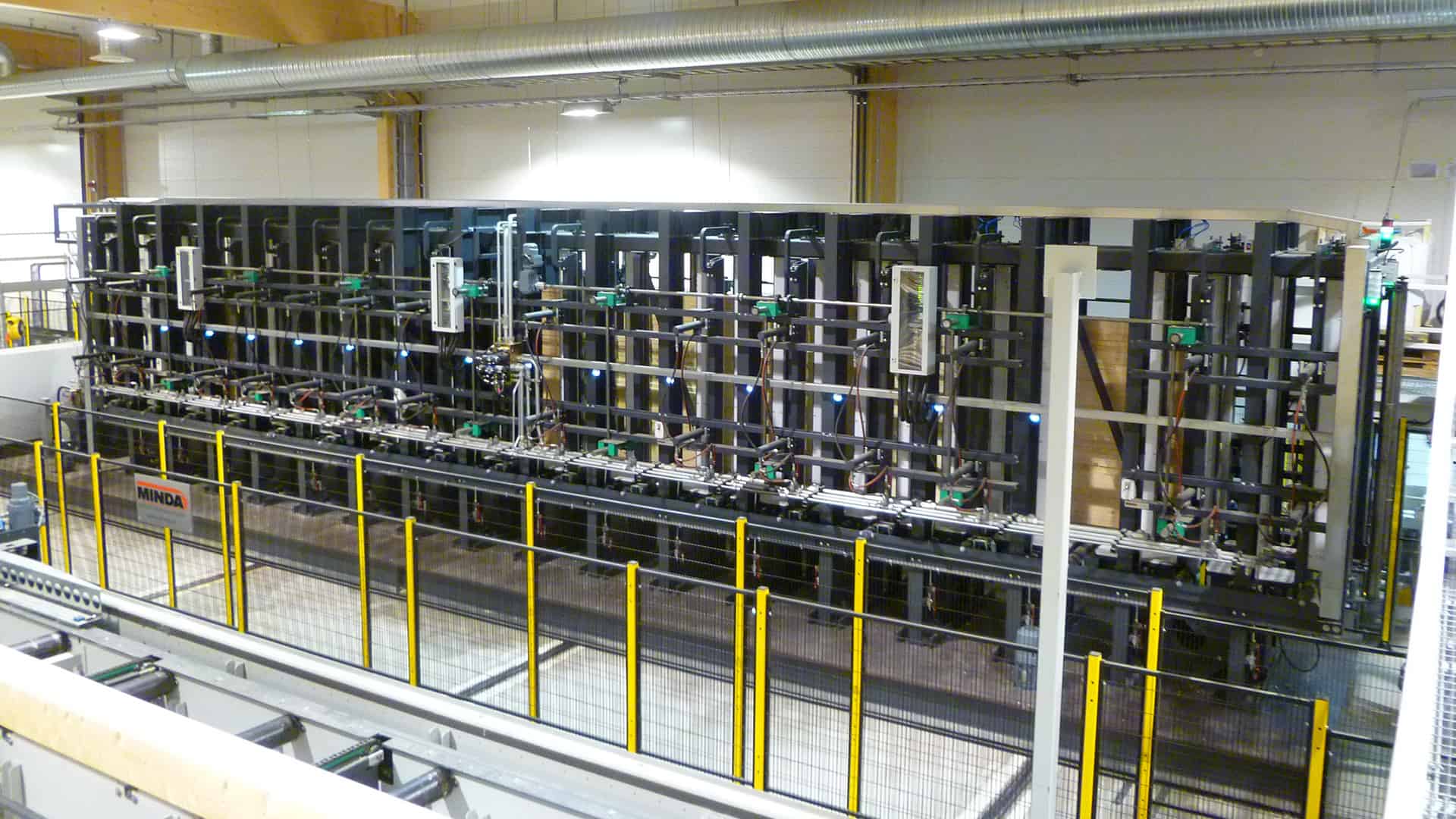
– The best grades are used for visible surfaces, but pieces with more branches can be used in the middle as well. The pieces are flipped in the glue machine such that the core side, which is able to withstand weather conditions the best, faces out.
The used polyurethane glue requires rapid movements – once the glue is applied, the log needs to be in compression within ten minutes. The log is compressed for 20 minutes, after which it is planed, profiled, and finally delivered.
NORTHERN WOOD IS SURE TO STAND
The northern wood used for Pölkky productions has dense grain, meaning that it grows only a little during a year. This gives it a good specific weight, achieving good strength and machining grades. The same trees growing in different parts of the country can vary greatly. In Southern Finland, trees grow quickly, and the undergrowth starts to decompose into black loose branches quickly. Northern trees have more branches, but the branches are generally more beautiful and healthy.
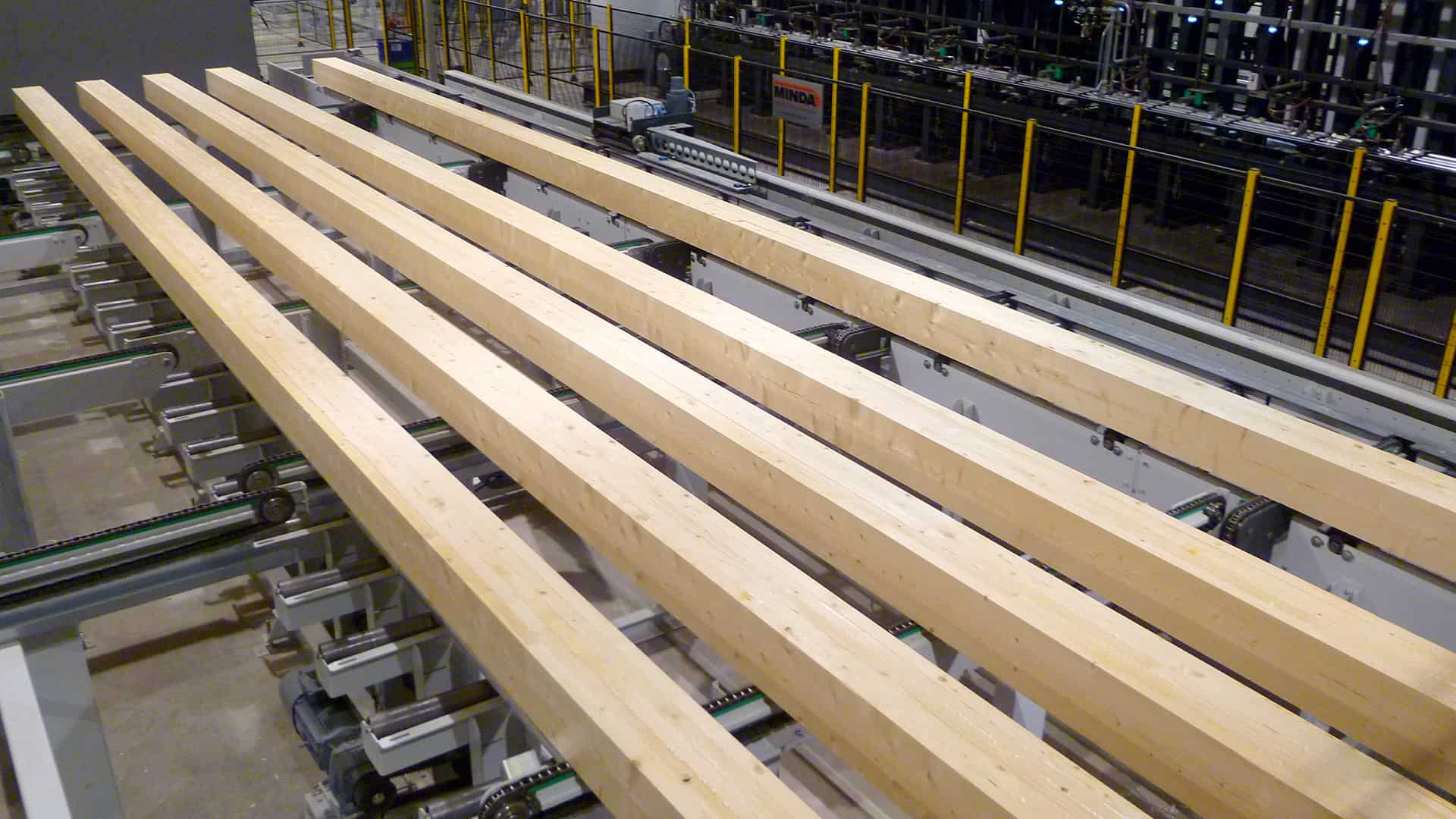
According to research by the Finnish Forest Research Institute, the best timber in terms of torsional stiffness is found in the North Savo and Kainuu regions. Rapid growth in the south reduces strength, whereas slow growth in the north increases damages caused by crown snow. These generate reaction wood, which reduces torsional stiffness.
– Wood is a fine material that presents nice challenges for the technical side of things as well, says Airisniemi.
Read more about northern wood.
Contact your nearest Kuusamo sales representative.
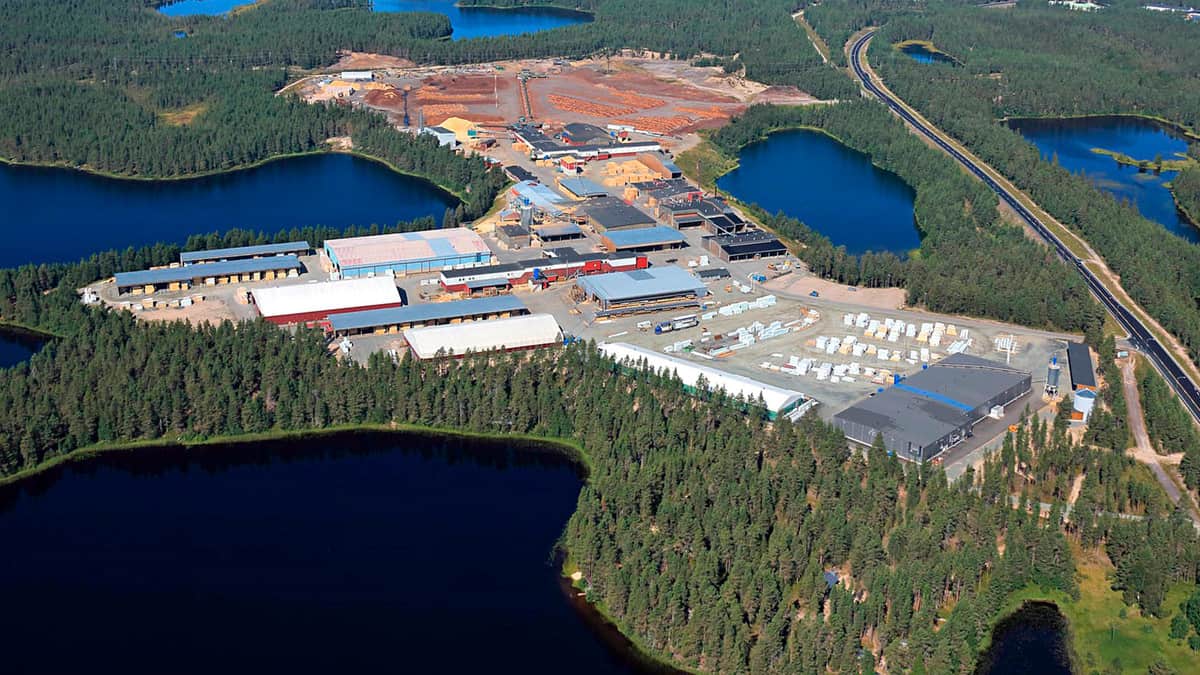
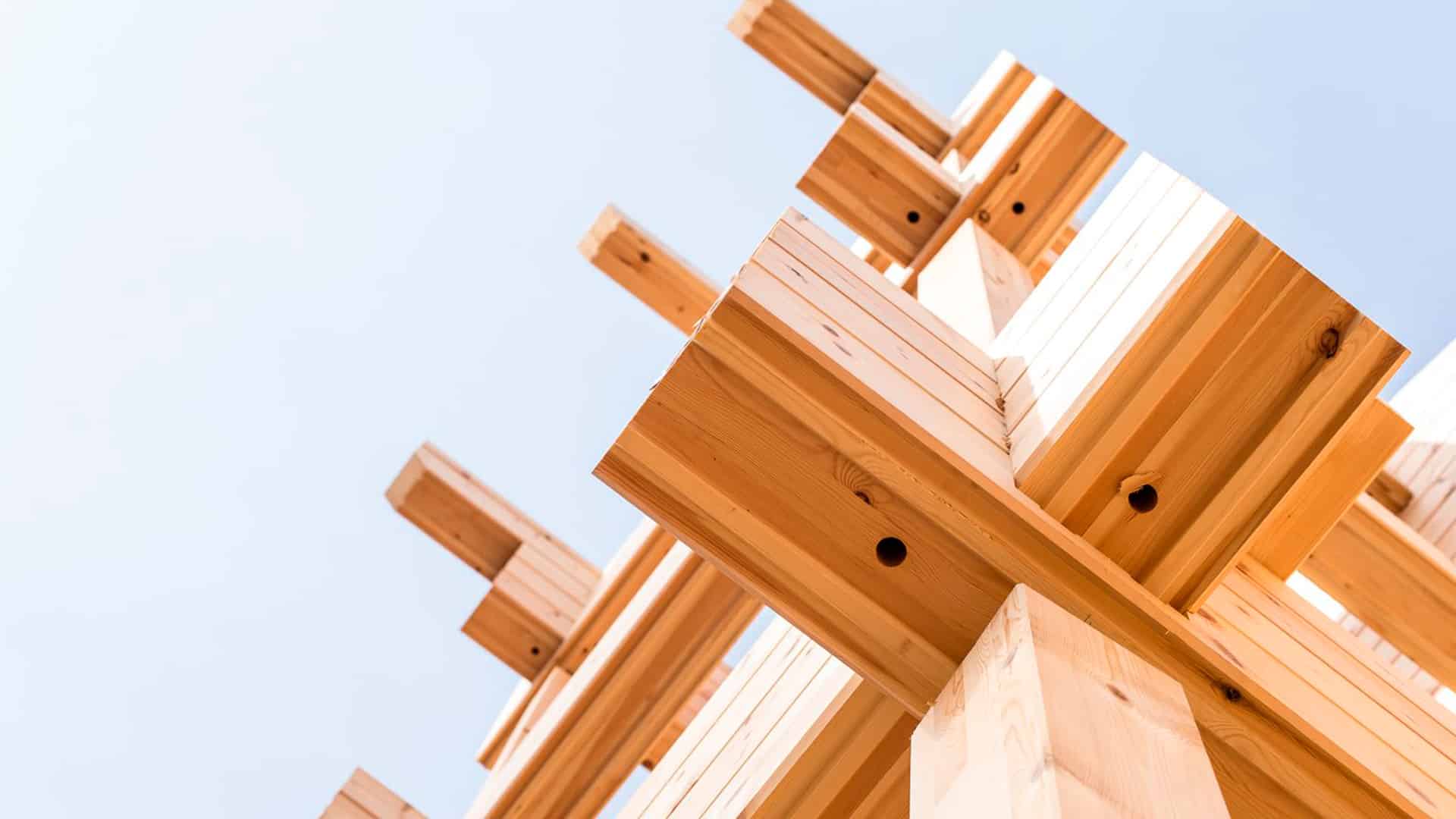